Analiza Ryzyka- jakie elementy powinna zawierać?
W dzisiejszym, dynamicznie rozwijającym się przemyśle, zagwarantowanie bezpieczeństwa pracownikom obsługującym maszyny jest priorytetem. Jednym z najważniejszych narzędzi, które pomagają osiągnąć ten cel, jest Analiza Ryzyka. Proces ten pozwala na zidentyfikowanie potencjalnych zagrożeń związanych z eksploatacją maszyn i wdrożenie odpowiednich działań minimalizujących ryzyko wypadków. W niniejszym artykule przybliżymy, jakie elementy powinna zawierać skuteczna Analiza Ryzyka dla Maszyn przemysłowych, by spełniała ona wszelkie wymogi prawne i branżowe.
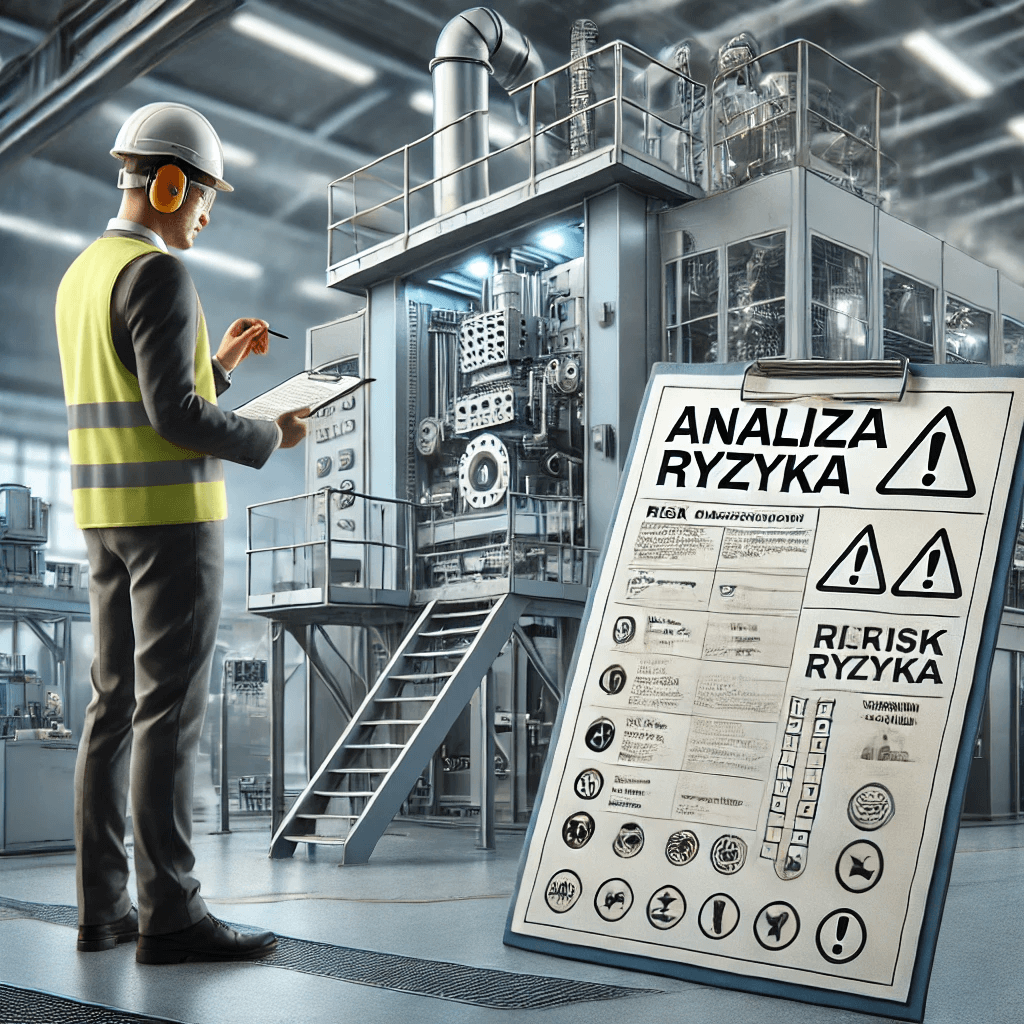
Definicja i znaczenie Analizy Ryzyka dla Maszyn
Czym jest Analiza Ryzyka?
Analiza Ryzyka to systematyczne podejście do oceny poziomu bezpieczeństwa maszyn przemysłowych. Polega na zidentyfikowaniu możliwych zagrożeń, oszacowaniu prawdopodobieństwa ich wystąpienia oraz wyznaczeniu skutków, jakie mogą one wywołać. Kluczową rolę w tym procesie odgrywają przepisy i normy, takie jak dyrektywa maszynowa 2006/42/WE, PN-EN ISO 12100 czy inne normy branżowe.
Dlaczego Analiza Ryzyka jest konieczna?
- Zapewnienie bezpieczeństwa: Maszyny przemysłowe często działają w trudnych warunkach i z dużą mocą, co stwarza wiele potencjalnych zagrożeń dla operatorów.
- Zgodność z przepisami: Unijne dyrektywy oraz krajowe regulacje wymagają, by producenci i użytkownicy maszyn przeprowadzali kompleksową Analizę Ryzyka dla Maszyn.
- Ochrona inwestycji: Skuteczna analiza pomaga zapobiegać wypadkom, co ogranicza koszty związane z przestojami, ubezpieczeniem i potencjalnymi roszczeniami.
Kluczowe regulacje i normy bezpieczeństwa
Dyrektywa maszynowa 2006/42/WE
W Unii Europejskiej głównym aktem prawnym dotyczącym bezpieczeństwa maszyn jest dyrektywa maszynowa 2006/42/WE. Nakłada ona obowiązek przeprowadzenia oceny ryzyka w procesie projektowania, produkcji i eksploatacji maszyn. Przepisy określają m.in. minimalne wymagania bezpieczeństwa, jakie muszą spełniać urządzenia wprowadzane na rynek.
PN-EN ISO 12100
Jednym z najważniejszych standardów opisujących proces Analizy Ryzyka jest norma PN-EN ISO 12100. Dokument ten definiuje zasady identyfikowania zagrożeń i oceny ryzyka, a także wskazuje metody zmniejszania ryzyka. Norma ta jest kluczowa dla producentów maszyn, a jej wdrożenie stanowi fundament skutecznej oceny bezpieczeństwa.
Normy branżowe i szczegółowe
W wielu sektorach przemysłu stosuje się dodatkowe normy branżowe, uwzględniające specyfikę danej działalności. Mogą to być normy związane z wybuchowością materiałów w branży chemicznej czy higieną w branży spożywczej. Analiza Ryzyka dla Maszyn musi uwzględniać również takie szczegółowe wymagania.
Podstawowe etapy skutecznej Analizy Ryzyka
Identyfikacja zagrożeń
Pierwszym krokiem jest określenie wszystkich możliwych zagrożeń związanych z pracą maszyny. Mogą to być zagrożenia mechaniczne (np. ruchome części, ostre krawędzie), elektryczne (porażenie prądem), chemiczne (substancje niebezpieczne) czy termiczne (ekstremalna temperatura). Na tym etapie warto skonsultować się z operatorami maszyn, którzy najlepiej znają codzienne realia eksploatacji.
Ocena ryzyka
Kiedy lista zagrożeń jest już gotowa, należy określić prawdopodobieństwo ich wystąpienia oraz skutki, jakie może nieść za sobą dany wypadek. Typowy model oceny ryzyka obejmuje:
- Określenie częstości występowania zagrożenia (np. b. mało prawdopodobne, prawdopodobne, bardzo prawdopodobne),
- Oszacowanie skutków (np. drobne obrażenia, poważne zranienia, śmierć),
- Przyporządkowanie poziomu ryzyka (np. niskie, średnie, wysokie).
Redukcja ryzyka
Po zidentyfikowaniu i ocenie ryzyka należy wdrożyć środki zapobiegawcze, mające na celu eliminację lub ograniczenie zagrożeń. Można to osiągnąć poprzez:
- Modyfikacje konstrukcyjne (np. dodanie osłon, blokad bezpieczeństwa),
- Zastosowanie systemów sterowania z zabezpieczeniami (np. czujniki, wyłączniki awaryjne),
- Ograniczenie dostępu do niebezpiecznych stref maszyny,
- Szkolenia operatorów w zakresie bezpiecznej obsługi urządzenia.
Dokumentacja wyników
Końcowym etapem jest sporządzenie dokumentacji zawierającej szczegółowy opis zidentyfikowanych zagrożeń, zastosowanych środków i wniosków z przeprowadzonej Analizy Ryzyka dla Maszyn. Dokumentacja ta stanowi podstawę do wykazania zgodności z normami i jest niezbędna podczas audytów czy procesu certyfikacji.
Elementy, które powinna zawierać skuteczna Analiza Ryzyka
Aby analiza była w pełni skuteczna i wiarygodna, powinna obejmować następujące elementy:
- Opis maszyny: podstawowe dane o urządzeniu, jego przeznaczenie, główne parametry techniczne, zastosowane systemy sterowania.
- Identyfikację zagrożeń: szczegółowe wskazanie miejsc potencjalnego ryzyka, mechanizmów powstawania zagrożeń, obszarów kontaktu człowieka z maszyną.
- Metody i kryteria oceny: jasne określenie, w jaki sposób i według jakich kryteriów dokonano klasyfikacji zagrożeń (np. matryca ryzyka).
- Ocena ryzyka: wskazanie prawdopodobieństwa i potencjalnych skutków wystąpienia zagrożeń, opisanie poziomu ryzyka (np. niskie, średnie, wysokie).
- Środki redukcji ryzyka: opis konkretnych działań minimalizujących zagrożenia, np. zastosowanie osłon, systemów bezpieczeństwa czy ograniczników ruchu.
- Wyniki końcowe: wnioski z przeprowadzonej analizy, wskazujące na poziom bezpieczeństwa maszyny po wdrożeniu środków zaradczych.
- Harmonogram wdrożenia: plan wprowadzania zmian w konstrukcji czy procedurach, tak aby osiągnąć pożądany poziom bezpieczeństwa.
- Aktualizacja i weryfikacja: harmonogram regularnego przeglądu analizy ryzyka i wprowadzania ulepszeń wynikających ze zmian technologicznych czy nowych wymogów prawnych.
Najczęstsze błędy w Analizie Ryzyka dla Maszyn
Podczas tworzenia Analizy Ryzyka mogą pojawić się błędy, które obniżają jej skuteczność:
- Niepełna lista zagrożeń: pominięcie nietypowych lub rzadko występujących scenariuszy.
- Brak precyzyjnych kryteriów oceny: ocena zagrożeń na podstawie subiektywnych wrażeń zamiast ustandaryzowanych metod.
- Niedostateczne środki zapobiegawcze: wdrożenie osłon czy systemów bezpieczeństwa, które nie pokrywają wszystkich zidentyfikowanych zagrożeń.
- Brak regularnej weryfikacji: analiza ryzyka powinna być powtarzana i uaktualniana wraz z rozwojem technologii, zmianami w przepisach czy modyfikacjami maszyn.
- Lekceważenie czynnika ludzkiego: niewystarczające szkolenia operatorów i personelu mogą prowadzić do zwiększonego ryzyka wypadków.
Rola personelu w procesie Analizy Ryzyka
Często niedocenianym aspektem jest zaangażowanie operatorów i personelu w proces Analizy Ryzyka dla Maszyn. To właśnie pracownicy mający bezpośredni kontakt z urządzeniem najlepiej znają codzienne praktyki i potencjalne zagrożenia:
- Operatorzy: dostarczają informacji o częstych błędach obsługi, specyficznych problemach czy awariach,
- Mechanicy i technicy utrzymania ruchu: wskazują na najczęstsze przyczyny usterek i trudności naprawczych,
- Dział BHP: dba o zgodność z przepisami, organizuje szkolenia i kontroluje procedury bezpieczeństwa.
Włączanie tych osób w proces identyfikacji zagrożeń i weryfikacji środków ochrony znacznie zwiększa skuteczność analizy.
Certyfikacja maszyn, a Analiza Ryzyka
Wprowadzenie maszyny na rynek unijny czy modernizacja istniejącego urządzenia często wymaga przeprowadzenia procesu certyfikacji, na przykład uzyskania znaku CE. Analiza Ryzyka jest jednym z podstawowych elementów tej procedury. Organy kontrolne i jednostki notyfikowane weryfikują, czy producent lub użytkownik maszyny:
- Przeprowadził szczegółową analizę,
- Dobrał odpowiednie środki ochrony,
- Udokumentował wszystkie działania w sposób zgodny z normami i dyrektywami.
Jeśli analiza została wykonana nieprawidłowo lub niekompletnie, istnieje ryzyko, że maszyna nie otrzyma certyfikatu, co w efekcie może prowadzić do wstrzymania jej eksploatacji lub wprowadzenia na rynek.
Podsumowanie
Analiza Ryzyka pełni kluczową rolę w zapewnieniu bezpieczeństwa maszyn przemysłowych, chroniąc operatorów i środowisko pracy przed potencjalnymi zagrożeniami. Aby była skuteczna, musi zawierać takie elementy jak precyzyjnie zdefiniowane zagrożenia, obiektywne metody oceny, działania redukujące ryzyko oraz regularną weryfikację i aktualizację wyników. Ponadto, Analiza Ryzyka dla Maszyn jest niezbędna w procesie certyfikacji – zarówno przy wprowadzaniu nowych maszyn na rynek, jak i przy modernizacji już istniejących urządzeń.
Wdrażając kompleksową Analizę Ryzyka, przedsiębiorstwa nie tylko minimalizują ryzyko wypadków i uszkodzeń sprzętu, ale także zapewniają spełnienie przepisów prawnych i norm branżowych. Współpraca wszystkich działów (inżynierów, operatorów, służb BHP i kadry zarządzającej) jest tu kluczowa, ponieważ pozwala na zebranie pełnego obrazu zagrożeń i wdrożenie skutecznych rozwiązań.
Zainwestowanie czasu i zasobów w profesjonalną Analizę Ryzyka jest zatem krokiem, który długofalowo przynosi korzyści w postaci wyższych standardów bezpieczeństwa, mniejszych strat produkcyjnych i lepszej reputacji firmy.
Jeśli masz pytania odnośnie Analizy Ryzyka – skontaktuj się z nami
Hi, this is a comment.
To get started with moderating, editing, and deleting comments, please visit the Comments screen in the dashboard.
Commenter avatars come from Gravatar.